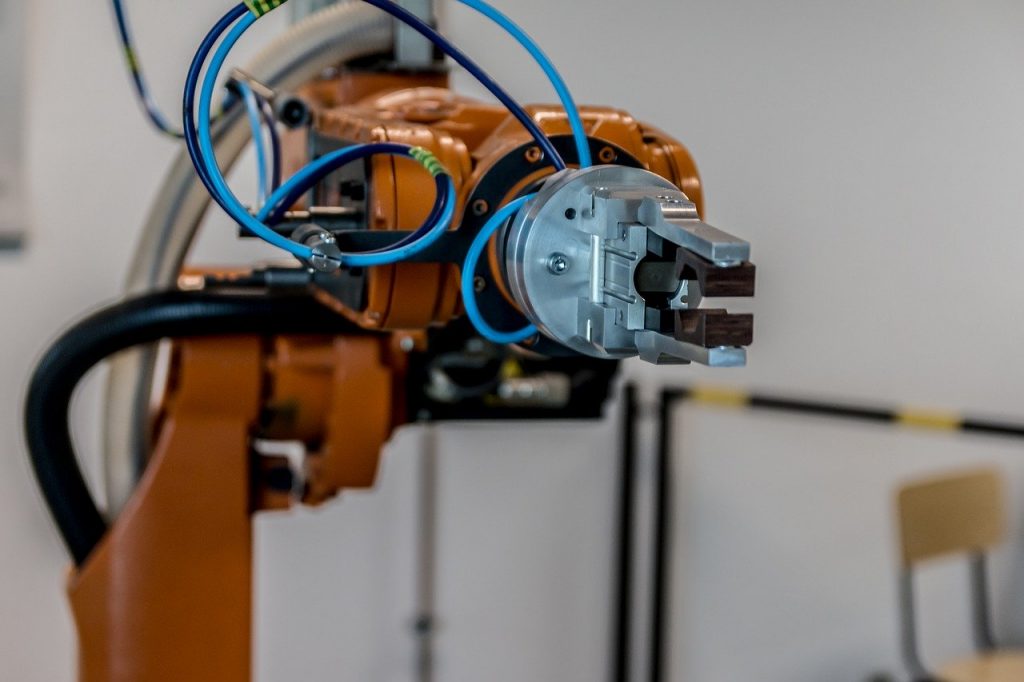
The future of cobots, or collaborative robots, is bright. Even before the COVID-19 pandemic increased the need for worldwide automation, the collaborative robot industry had an expected annual growth rate of nearly 30%. The market expected to reach $5.6 billion by 2027.
This exponential growth is due in no small part to industries like automotive and industrial assembly. Pick and place needs and material handling contribute, too. These fields account for 75% of all cobot-related revenue from 2018. As the market continues to expand, these uses are expected to hold a full 2/3rd of the cobot market.
Expanded technology is the primary driving force behind this exploding market. Industrial robotics that was once caged to protect human workers have now been allowed additional freedom. This is due to vision integration systems that offer obstacle avoidance. Such systems were featured in the Automate 2019 Show in Chicago, have significantly expanded how cobots can be integrated into today’s smart factory.
The History of the Cobot
The term “cobot” stems from a 1997 US Patent filed by James E Colgate and Michael A Peshkin. The patent was entitled “Cobots” describing the “field of software-programmable robotic manipulators and assist devices….that can directly interact with a human operator.” The device they describe in their patent is what we today would describe as an IAD or an Intelligent Assist Device. It was based upon previous work done by General Motors (GM) to add robotics to their workforce.
This research also used previous successes in building articulated industrial robots powered by electric motors or other means. These moved at points using a range of structured joints that allowed the robot to spin, bend, or grip. The joints are similar to human wrists, elbows, and knuckles. However, human constraints don’t apply. (1)
Colgate and Peskin’s device was capable of moving in a non-caged environment as it helped human co-workers with assembly operations. However, the device had no internal source of motive power as a safety precaution. Instead, this power was provided by a human worker. Later cobots like KUKA’s LBR3 and LBR4 moved under their own motive power but was still more IAD than cobot.
The first truly collaborative robot with the capability to work safely alongside human workers without safety fencing was Universal Robots UR5, released in 2008. Thesis small, user-friendly cobot launched a new era of cost-efficient integration, giving small- to medium-sized manufacturers an avenue to this technology without exorbitant investment.
In many cases, cobots were initially met with skepticism and suspicion by those in the manufacturing industry, and some were slow to consider the adoption of this technology. Now, however, the market is growing rapidly.
Challenges for Cobot Adoption
Although cobot technology is developing quickly, there are still a number of challenges standing in the way of industry-wide adoption. One of the most significant is the limited dexterity of all robotics, that can struggle with small or delicate parts with different surfaces and shapes depending on position. For now, this limits many cobots’ ability to choose pieces quickly enough to maintain a proper production pace.
But faster processors attached to cobot vision systems address these challenges head-on. These systems process spatial data at faster speeds, allowing cobots to maintain motion control and improve productivity. Cobots can more easily identify paths around obstacles, too. This improves safety. The machine can change its actions without a reduction in work speed.
This improved vision allows less part precision and positioning. Unlike previous generations, new cobots can “see” and adjust more like live workers. Additionally, cobots can adapt to environmental changes as they happen, such as a human worker moving into their path, without incident. This maximizes the safety of human workers, but it also allows multiple moving cobot units to interact with each other on the manufacturing floor as they perform independent tasks, without fear the expensive units will inadvertently run into one another.
How the Pandemic May Affect the Future of Cobots
Many companies have seen business plummet in the wake of the pandemic. But some manufacturers–especially those who have pivoted to provide PPE or other necessary equipment–have actually seen an increase during this time. And yet as companies work to decrease the risk of exposure to workers, maintaining pre-pandemic levels of production has become a challenge.
Cobots have provided the solution for some. RCM Industries, an aluminum die casting manufacturer with a seven-decade history, added two UR10e cobots to their manufacturing floor(2) in order to move employees to safer tasks, to maintain social distancing, and to increase their ability to compete with overseas competition. The company has seen a 15% increase in throughput since adding the cobots to their operations.
While no one has a crystal ball to see what will happen in the manufacturing industry in the future, it seems more than likely cobots will continue to increase their foothold. Depending on the future needs for social distancing and worker safety, this adoption may accelerate even more than previously expected.
Visit our main site to search our inventory for GE Mark I, II, IV, V, and VI turbine control replacement parts.
(1) http://motion.cs.illinois.edu/RoboticSystems/Kinematics.html
(2) https://www.rcmindustries.com/rcm-industries-universal-robots-fleet/
One reply on “History and Future of Cobots”
[…] Companies will compete for employees with advanced digital skills, extended computer skills, an understanding of cobot systems, and robot/automation programming skills. It may become increasingly difficult to find […]